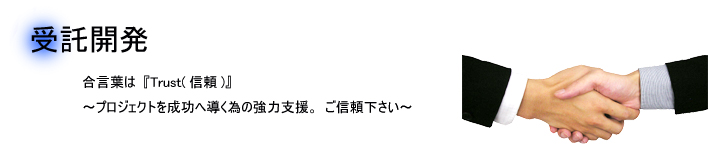
初めてのお客様とお付き合いを始めさせて頂くきっかけとして、一番多いのは『相談』です。
とにかく困ったことを投げかけて頂ければ解決へ導かせて頂きます。
このページでは、そんなお客様の『困った』を解決させて頂いた事例の一部をご紹介します。
事例9:工業製品なのに再現性なし?〜画像処理エキスパートの『人間学習』〜
事例7:PCレスの試作機開発〜アルゴリズム開発から詳細設計まで〜
事例6:アルゴリズム開発ビジネス〜機能実現の相談から全てを完成させるまで〜
事例5:画像処理の総合コンサルタントA〜ハードウェアのつもりがソフトウェア〜
事例4:画像処理の総合コンサルタント@〜ハードウェアとソフトウェアの切り分け〜
◆お客様の悩み◆
工場で大量生産している製品ですが、二つと同じ模様にならないランダム性が『付加価値』の製品なのです。
このランダム性が『検査』には邪魔になり、現在でも人間が検査する方法に頼っています。
トレーサビリティの観点からも、検査基準の明確化のためにも、『画像処理』で検査できませんか?
◇解決方法◇
対象物は、織物でした。
繊維の毛羽立ちなど、工業製品なのにすべてCADで設計した通りに仕上がるものではありません。
そのランダム性が製品の付加価値を高めているので、一様な製品が製造されるようにするのは本末転倒です。
解決に向けての大きなヒントは現状行われている『人間検査』でした。
1製造ラインの検査工程に、大勢の検査要員が『人間検査』を行っていました。
タクトタイムの為に大勢の検査要員が必要となってましたが、それぞれの方に『どんなものを不良としてますか?』とヒアリングを行って頂きました。
お客様の生産管理(自社内向け生産技術研究所様)の方が、根気よくヒアリングを行って頂けたことがのちの『解決手段』の構築にとても役立ちました。
ヒアリング結果を、検査要員の方の言葉と製造上の不良原因の関連付けを行って頂きました。
それと同時に、画像処理側では対象物の画像データに対して、大量の特徴量(100種類以上の特徴量)をデーターベース化しました。
最後の仕上げは、大量の特徴量データベースと実不良画像との関連付けを重み付けスコア化しました。
実際の検査タクトタイムを考慮し、関連付けの際の重みが低い(関連が薄い)特徴量を計算対象から外し、人間と同等の検査を安定的にできるようになりました。
このケースのポイントはヒアリングです。
処理の流れ的には『機械学習』の辞書作成に似ていますが、従来の検査基準と変えない為にも『検査要員からのヒアリング』がポイントとなりました。
流行りの機械学習ですが、生産管理のエキスパートと画像処理のエキスパートが知恵を絞って『人間学習』させた例です。
◆お客様の悩み◆
これまで『肌診断』の専門家が、たくさんの方の肌を見てお肌の状態を診断してきました。
しかし、専門家の育成はとても大変で、一日に診断できる量が限られてしまいます。
肌診断の専門家が、どんな点を見て、どのように診断結果に反映されているかをまとめる事は、簡単にいかないと思いますが、画像処理で何とかなりませんか?
◇解決方法◇
まずは、実際に『肌診断』の専門家の方が行っている作業を見せて頂きました。
そこでは、3〜4項目程度の内容を各5段階評価していました。しかし、総合判定はかなり細かいもので、各項目の5段階評価以外に、何か脳の中で総合判定に影響されているものがあると考えました。
流石専門家ですね!同じサンプルを見ると、常にほぼ同じ総合点を付けられるので『この人の基準を引き出そう』と決めました。
そこで、3つのステップを踏んで本件の解決を行うプランニングを決めました。
1.多数のサンプル(100種類)を用意して頂き、それらのサンプルに対して、評価結果を知らない画像処理エンジニアが、たくさんの種類の特徴量を抽出しました。たくさんとは、100以上の異なる特徴量です。
2.肌診断の専門家が作成した総合評価と、画像処理エンジニアがプログラムで作成した特徴量を、どちらもグラフ化しました。グラフ化に同じ傾向(又は真逆な傾向)がある特徴量と、無関係な特徴量に分類しました。
3.『同じ傾向にある』として生き残った特徴量を対象に絞り、専門家の総合判定との類似度で、特徴量の重要性を自動調整し、複数の特徴量から、自動的に総合判定する『肌診断エンジン』を作成し、新たなサンプルを与え自動チューニング(方法は非公開)を行い、完成しました。
人間が見て判断しているものはたくさんあると思います。
事前ヒアリングで、同じサンプルを見て、毎回同じような評価が出来ている事から、『頭の中にある評価基準を引き出す』事が可能となりました。
人間ですので、同じサンプルを見ても、異なる結果が出てしまう事もあるでしょう。
異なる結果が出てしまうものだったら、コンピュータも結論を出せなかったと思います。
◆お客様の悩み◆
ある商品の開発で画像処理部を担当しています。PC上で色々な実験ができる汎用ツールを使って、
どんな処理を組み合わせれば企画した製品が作れるかを実験検証するフェーズを終えたところです。
しかし、自社製品にPCや汎用ソフトを使う事は現実的ではなく、
さらに新規事業のため社内でエンジニアをアサインできません。相談に乗ってくれませんか?
◇解決方法◇
アルゴリズム開発と、回路設計&ソフト設計とのコミュニケーションギャップが課題でした。
当社でも同一人物がアルゴリズム開発から、回路やソフトの設計まで可能なわけではありません。
そこで、社内のアルゴリズム開発の担当者をお客様とのコミュニケーション担当としてアサインし、
理解したことを社内のハードエンジニアやソフトエンジニアに相談しながら仕様を作成していきました。
ハードやソフトの視点からは、演算精度がどこまで必要なのか?という回答次第で、回路規模や組込CPU性能が異なるということが課題になりました。アルゴリズム担当としては『演算精度が高い方が良い』との見解でした。
では、実際の製品性能としてはどうなのでしょう?
結果的には製品コストを考え、24ビット浮動小数点のところ(組込CPU処理)と、64ビット固定小数点のところ(FPGA処理)に変更しても、製品性能として許容できる結果であることが判明しました。
その結果、演算をFPGA化し、CPU+FPGAの組込機器として実現することができました。
このケースのポイントはチーム力です。
汎用ツールの内部では、64ビット浮動小数点を使っていることが多いですが、
製品化時のコストを考えると、少しでも精度を落とした計算で済ませたいものです。
この配慮をアルゴリズム開発フェーズに求めてしまうと、自由な発想が出てきません。
しかし自由な発想から産まれた新しい処理でも、製品化時にはコストを意識した再設計が必要です。
異なる能力が必要ならばチームで解決しましょう。足りないと思われるところをフォローする事で、
当社とお客様とのチーム力でより良い製品を世の中に出していくことが可能になります。
◆お客様の悩み◆
カメラで連続した画像を撮影しています。
連続した画像なので全部つなぎ合わせて大きな画像に出来ると思ったのですが、
何故か市販ソフトだと変な位置につながってしまいます。何とかなりませんか?
◇解決方法◇
初めのお問い合わせでは『コンサルティングとして依頼できるか?』という内容でした。
そこで打合せの際に、何に悩んでいるのかを実際に目の前で実現して頂きました。
お客様がカメラである対象物を連続して撮影すると、それらがつながったパノラマ写真が作成されていました。
ところが撮影したい対象は、特殊な環境で特殊な部位を撮影するものでした。
成功するケースと失敗するケースの画像データを頂き、社内で実験プログラムを作成したところ、結果は同様になりました。
すなわち、失敗する原因がある事がわかりました。失敗する場合は、画像に連続性が無く撮影角度も異なるものでした。
そこで、お客様の目的を達成するための手法開発のご提案(これがアルゴリズム開発になります)を行い、手法開発のためのアプローチ案を提示してご承認を頂きました。
この時点ではご希望の処理が実現できるか否かが成果であり、処理が実現できた場合でも、処理速度などの高速化は次のフェーズになる事をご了解頂けたので、アルゴリズム開発としてのビジネスが成立し開発スタートできました。
その後、無事にお客様の満足される処理が完成し、次のフェーズとして『高速化』を行い、お客様の最終用途にマッチしました。
このケースのポイントはお客様が満足できない原因の調査が大切という点です。
処理が失敗することを実験で再現できなければ、解決方法に踏み込めなかったでしょう。
さらに過去の成功手法にとらわれないために、一旦処理速度を無視した『成功精度最優先』の手法を確立し、
その後に同一精度を維持しつつ高速化するアプローチを行った事が、成功できた理由だと思います。
アルゴリズム開発は、プロジェクトをスタートする時点で成果を約束できない、商談としては難しいビジネスです。
リスクと成果をお客様と共有することで、ビジネスとして難しいアルゴリズム開発もビジネスにつながります。
◆お客様の悩み◆
高速なラインセンサを使用して、画像取り込み&計測する製品の試作機を開発したい。
取り込みや画像処理速度が速いので、タクトタイムを考えると実現手段はハードウェアが適切か・・・!?
開発見積を依頼するための要求仕様を作ってみたものの、検討している画像処理手法を実画像でテストしたことがなくて心配だ!!
後からアルゴリズムに大きな変更が入ると、ハードウェアは改版しなければならず無駄な費用が発生しがちだし・・・。
スケジュールの余裕もないし・・・。何とかなりませんか?
◇解決方法◇
商談時のヒアリングからお客様の要求を整理してみると、今回のミッションは『実時間で処理できることを調査する試作機の開発』であることが分かりました。
そこで、提案させて頂く予定だった『大規模FPGA搭載のPCI Expressボード』から『マルチコアCPUを搭載したPCを複数台使ったソフトウェアシステム』へ変更、さらに処理性能が不足する場合には『GPUプログラミングを用いた高速化』も併せて提案させて頂きました。
これならハードウェアの開発よりも費用を抑えることができ、後から処理部を変更するにも柔軟な対応が可能です。
ただし、このアプローチにはデメリットもあり、
などをお伝えしましたが、結果的にこの案件は『試作機の柔軟性』が最優先であり、試作機の追加はないと判断されたため、ソフトウェアの開発案件として成立しました。
このケースのポイントは、要求の理解力と異なる視点からの提案力です。
ご相談当初からハードウェア、ソフトウェアの両担当が商談に入り、お客様と一緒に充分議論することで、要求を深く理解し、
『お客様にとっての優先順位』を整理させて頂き、より良い提案に繋げることが出来ました。
当社では技術担当者が直接お客様とお話させて頂ける体制を作っていますので、最初の商談から深い話が出来るのです。
◆お客様の悩み◆
新規の画像処理アルゴリズムを開発したので、それを使った新製品の試作を開発したい。
でも、このアルゴリズムはハードウェアとソフトウェアのどちらで実現するべきなんだろう?
とりあえず、ハードウェア開発が得意なH社と、ソフトウェア開発が得意なS社に話を聞いてみようか。
・・・というよりむしろ、それも含めて相談出来るようなコンサルタント会社はありませんか?
◇解決方法◇
まずはお客様のアルゴリズムの内容をヒアリングさせて頂くことから始めました。
そしてハードウェアの担当者とソフトウェアの担当者が、それぞれの切り口からアプローチし、議論を交わします。
こちらの案件ではアルゴリズムの一部にラベリング処理が使われていた為、この処理をハードウェアで実現させるか?ソフトウェアで実現させるか?の議論になりました。
ソフトウェアの場合、対象ラベル数が少ない事が保証できれば高速化出来る手法もあるが、ラベル数に比例して処理時間が遅くなります。
一方ハードウェアの場合、ラベル数に関わらず処理時間が一定になるので、ラベル数が少ない事を期待して良いかがハードウェアとソフトウェアの切り分けのポイントとなりました。
お客様によれば、入力画像のラベル数が保証できない事が確定し、さらに装置としては処理時間を第一優先としたいとのこと。
その結果、当社が持っているハードウェアIPで実現する事に決定し、ハードウェア化をメインに当社製品+ハードウェアIPというカスタマイズ案を提案させて頂きました。
このケースのポイントは、ハードウェアとソフトウェアの切り分けです。
当社にはハードウェア、ソフトウェアの各担当がカバーし合える環境があります。
また、既存製品、ハードウェアIP、ソフトウェアライブラリなどの資産と過去の実績から最適な道を選んで提案することが出来るのです。
◆お客様の悩み◆
開発会社は沢山あるけれど、いずれ製品が量産化される事を踏まえて開発時から相談出来る会社はないだろうか。
開発と量産の委託会社が違うと、色々手間と時間がかかるし・・・。かと言ってどこに相談して良いのかも分からない。
量産と言っても、恐らく1ロット10台〜100台ぐらいの規模だし・・・。場合によっては、数台って事もあるかもしれない。
出来れば、開発時から量産化の相談もしたいのですが・・・。何とかなりませんか?
◇解決方法◇
このお客様はLSIの開発が専門だった為、基板での製品開発は初めてでした。
しかも、設計だけでなく量産も委託できる開発会社を探さなくてはならず、当社へお話頂くまで苦労された様です。
量産に繋がる場合に気配りが必要となる「入手性、最低購入数」を考慮した部品選定についてなどを開発段階からお伝えし、開発から量産までをお任せ頂くことができました。
結果、長いお付き合いとなり、複数のアイテムを担当させて頂きました。
このケースのポイントは開発から量産までの一括委託です。
1ロットの数が多い量産であれば開発と切り分けるメリットが多くなりますが、少量のロットでは一括委託の方が良い場合があります。(当社実績:500台/ロット)
開発から一貫して行うことで、量産時にも全てのボードに対して、製造検査だけでなく機能検査まで全てをクリアしたボードを納品させて頂きます。
稀にあるケースとして「お客様の認定工場でないと製造委託出来ない」という場合は、生基板、実装工場それぞれのISO認定書・品質管理規定を提出や、各工場への立会い検査などにも対応実績が御座います。
また、納品後にお客様がボードを壊してしまった際にも解析や修理がスムーズに行え、仮に部品が製造中止になっ場合などには直ぐに代替部品をご用意することができます。
結果、予想以上に製品寿命が延び、長期に渡って量産が続いたケースも珍しくありません。
量産をお考えの場合は数量の多い少ないに関わらず、まずはご相談下さい。
◆お客様の悩み◆
そういえば、KITに開発を依頼している画像処理ボードを収めるPCを、そろそろ探さなくては。
確かフルサイズのPCIボードが3枚で・・・OSを動作させるためにマザーボードのチップセットは・・・。
と色々調査して無事にPCが見つかったけれど、量産化されたとたんにマザーボードが製造中止!?
振り出しに戻って、PCの選定から始めなくてはいけない状態に・・・。
これから先、マザーボードが生産中止になる度に調査をすることになるのか・・・。何とかなりませんか?
◇解決方法◇
当初、当社が開発を委託された範囲は画像処理用のPCIボードのみでした。
画像処理ボードを収めるPCは、お客様が別途手配されている状況であり、マザーボードや筐体が生産中止になる度にお客様側での選定・動作確認が必要となり頭を悩ませていました。
そこで量産の段階で、当社が提案したのは『画像処理ボードセット開発〜PC込みの一括受注〜』です。
もともと自社で開発したボードですから、ぴったりマッチするPCを探すのはお手の物。
PCIボードだけでなくPCもセットでご依頼頂くことによって、お客様側でのPCの選定・ボードの取り付け・動作確認の工数を大幅に削減することができました。
また不具合が起こった際に、『画像処理ボード側の不具合』か『PC側の不具合』か『双方の相性問題』かを判断するのはとても大変なことです。
こういった場合、PC込みで開発を依頼して頂くと調査は一括して当社が行いますので、お客様も安心してご依頼頂けます。
このケースのポイントはPC込みの一括受注です。
開発の際、お客様側でのPCの選定・取り付け等が困難な場合は、当社で一括しての受注が可能になりますので
まずはご相談下さい。※PCのみならず、最近ではボードに合わせた筐体の設計にも力を入れております。
◆お客様の悩み◆
センサ自体を開発中だが、営業サイドから展示会への出展を要求された。
センサだけを展示しても効果は薄いので、取得した画像を見れるようにしたいらしい。
しかし、現段階では試作なのでフルカスタムでボードを起こすほどの予算は取れないし、スケジュール的にも厳しいし・・・。
I/Fが特殊なので汎用性のあるキャプチャボードを買って来ることも出来ない。何とかなりませんか?
◇解決方法◇
当社の『Getter』シリーズを使用することで短納期、低コストで解決しました。
この『Getter』という基板はPCIもしくはPCI Expressのボードで、グレードの違うFPGAを実装した開発素材用の製品です。
出荷時のFPGA回路は、PCIのI/Fやメモリコントローラなど、基本的に必須且つ最低限の回路規模で構成されることで、多くの回路リソースが空いていますので、自由に処理回路を追加が出来る事が特徴となっています。
今回の場合も空いている回路リソースを利用し、センサから出力されるベイヤーデータに対してFPGAの回路で画像処理を施しました。
これによってセンサの生画像を展示会向けの綺麗な画像に変換することが出来たのです。
また、I/Fの問題は子基板で解決しました。
『Getter』にはFPGAのIOピンが直接接続できる子基板I/Fコネクタが付いており、専用子基板を開発するだけで自由なI/Fを持たせることが可能なのです。これならフルカスタムよりも短期間、低予算で作成が可能ですね。
このケースのポイントはI/Fです。
短納期、低予算では完成品を流用する方法が有効的ですが、I/Fが特殊だった為に悩まれてしまいましたね。
こうして無事に展示会を終えられたお客様ですが、作成した評価用ボードセットはセンサの営業ツールとしても活躍したそうです。